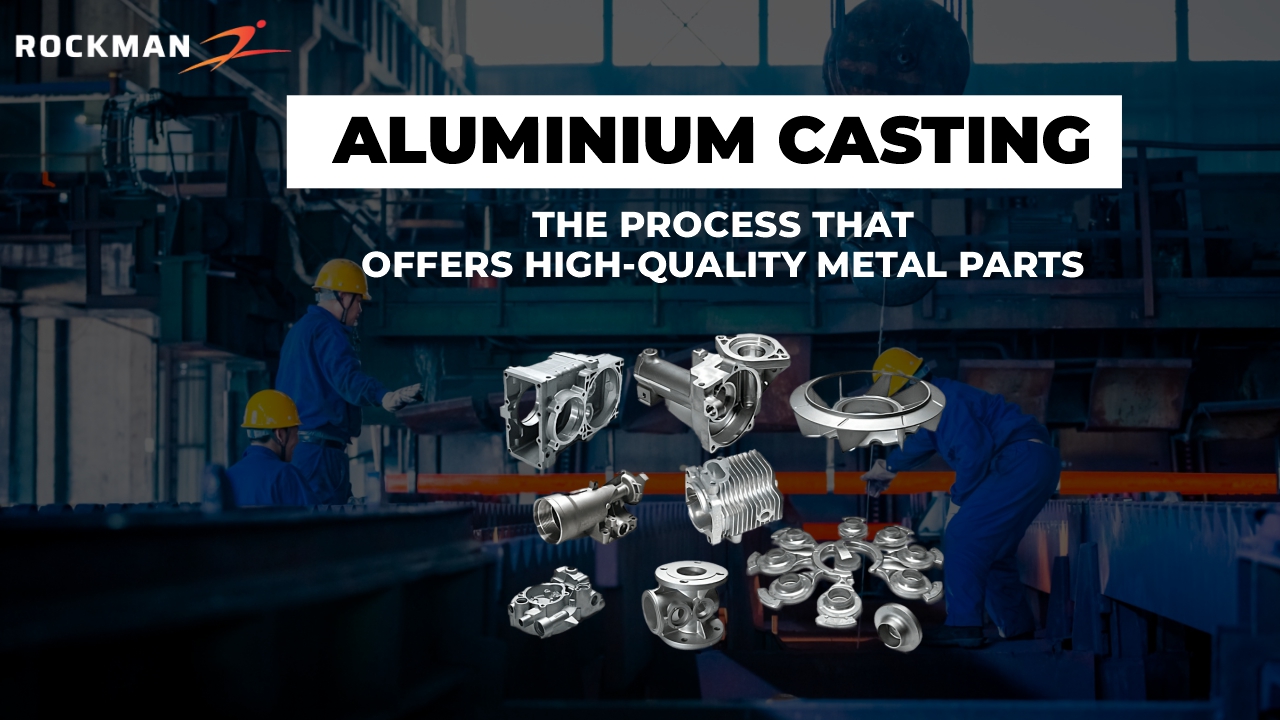
Aluminium die casting is a proven process for creating highly accurate, high-quality parts for a variety of applications that precisely meet the design parameters. Die casted alloys made of aluminium are strong and lightweight, and they offer good dimensional stability for parts with intricate geometries and thin walls. In comparison to other non-ferrous materials, aluminium die cast parts have more surface finishing options and can sustain higher working temperatures. Die cast aluminium components have excellent rigidity and strength-to-weight ratios, are highly conductive, and are resistant to corrosion.
Aluminium die casting process
In aluminium die casting process, an aluminum bar is heated and melted entirely at a high temperature and then forced into the pre-shaped mold cavity to create desired metal parts. The cold chamber of the casting machine is used in the aluminium die casting process.
In the cold chamber machine, the melting pot is separated and the molten aluminum alloys then are ladled from the pot into the die either under gravity or under high pressure. Then, you need to separate the two halves parts of the mold to reveal the aluminum cast part.
The process can be highly automated with little manual intervention required and making it ideal for producing parts at large volume and low cost in industries such as Automotive, Aerospace, Construction and Electronics Industry.
Aluminium die casting is carried out mainly through three types of process:
High-pressure Die Casting
The manufacturing process of high-pressure die casting (HPDC) is incredibly effective for creating a variety of product types. In this process, molten metal is forced at high speed, and high pressure into a closed steel die cavity. Both of the die are stationary and moving halves are mounted to the platens of the die casting machine. The molten metal is injected into the closed steel die at the injection end of the die casting machine using hydraulics and pressurized gas.
Compared to other manufacturing processes, high-pressure die casting is an efficient, economical process that:
- Produce strong, lightweight parts that require less machining than fabricated parts
- Create complex and intricate shapes in a single piece, eliminating the need for assembly or welding
- Offer a broader range of shapes than other metal manufacturing techniques
- Achieves close tolerances
Low-pressure Die Casting
Low-pressure die casting uses pressure (typically around 0.7 bar) – rather than gravity – to fill molds with molten metal. In this process, the holding furnace is located below the cast and the liquid metal is forced upwards through a riser tube and into the cavity. The pressure is applied constantly, sometimes in increasing increments, to fill the mold and hold the metal in place within the die until it solidifies. Once the cast has solidified, the pressure is released and any residual liquid in the tube or cavity flows back into the holding furnace for “recycling.” When cooled, the cast is simply removed.
Low Pressure Die Casting allows precise control of the filling process. Injecting the molten metal in this way reduces oxide formation and reduces porosity, ensuring superior consistency from top to bottom. As such, low pressure casting results in exceptional density and strength values as well as excellent dimensional accuracy. While this method is greatly suited to simpler, symmetrical forms, more complex geometries can be achieved with the use of sand cores within the molds. With the advantage of uncomplicated machinery and technology, the low pressure die casting process lends itself well to automation.
Gravity Die Casting
Gravity Die Casting is a permanent mold casting process, where the molten metal is poured from a vessel or ladle into the mold. The mold cavity fills with no force other than gravity, filling can be controlled by tilting the die. Undercuts, and cavities can be incorporated into the component form with the use of sand cores.
Advantages of this process include the possibility of low gas porosity, and fine grain sizes can be achieved.
Rockman Industries has been into Aluminium Die Casting since the last two decades and is one of the top manufacturers equipped to follow the three types of die casting processes in India. Quality management, safety protocols and focus on environmental sustainability is at the core of Rockman’s manufacturing principles.